How to Choose Safe and Effective Emergency Eyewash Units?
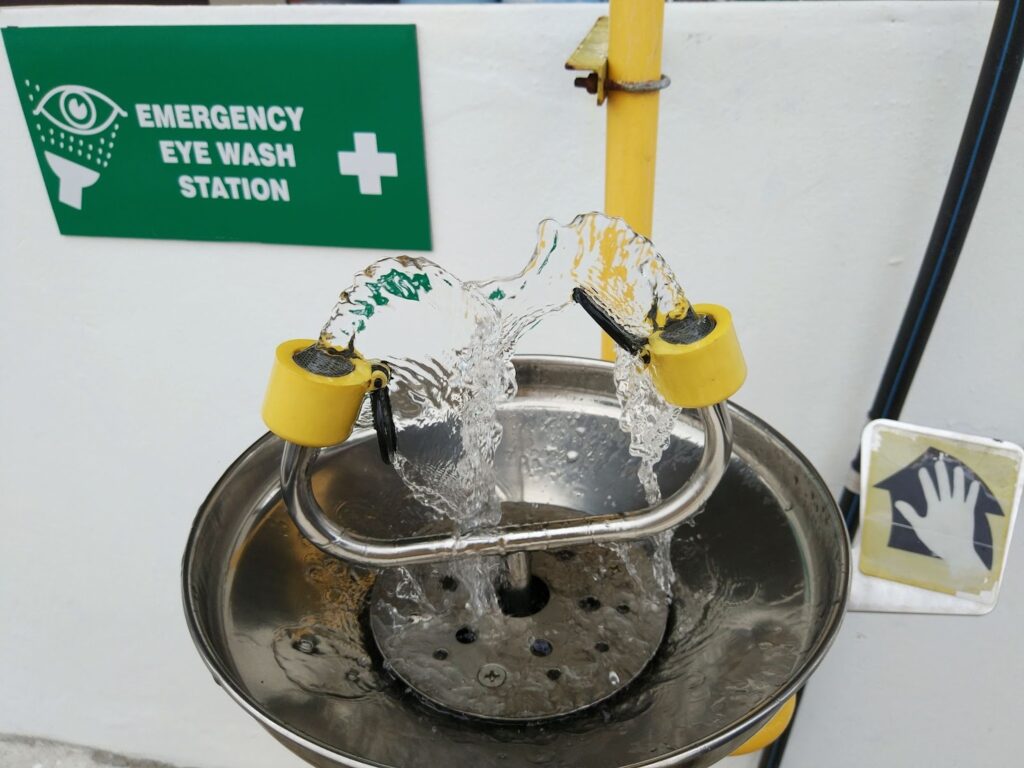
The human eye is susceptible to serious injury from foreign materials, whether solids or liquids, such as:
- Dust
- Chemical liquids
- Chemical vapours
- Metal shavings
- Ultraviolet light
Many workplace environments call for eye protection like safety glasses or goggles — some settings even require a full face shield or helmet. Safety programs exist to ensure organisations meet the standards set forth by Safe Work Australia and Workplace Health and Safety programs, and workers are protected. Even with the most stringent precautions in place, accidents can still happen. When a workplace accident occurs, it’s essential to minimise its effects using a safe and effective treatment as fast as possible. If an accident involves foreign liquids or other materials getting into the eyes or elsewhere on the body, having an emergency eyewash unit, or “eye washer”, and drench shower is vital.
In this post, you’ll learn the standard requirements for eye washer stations and how to choose the emergency eyewash unit that’s right for your workplace.
What are the standard requirements for an eyewash station?
Standards Australia (SAI) creates workplace standards for all industries in the country. Australian Standards for emergency eye washing and shower stations established the minimum performance necessary for eye-washing equipment and drench showers. In the event of an eye, face, or body exposure to dangerous materials or chemicals, consider the following guidelines for your organisation’s emergency eyewash units and showers:
- Placement. The most critical time after chemical exposure is within the first 10 to 15 seconds. Eyewash stations should be located no further than 10 seconds from points of potential hazardous exposure. For highly hazardous materials, these units should be within steps of the point of potential harm. Emergency stations should be easy to reach without obstructions, such as stairs or islands.
- Visibility. The location of emergency drench showers and eyewash stations should be well lit and marked with clear signage.
- Water supply and temperature. SAI requires workers immediately flush their eyes with water after any hazardous chemical contact. The water supply must be portable, a saline solution, or another medically appropriate solution. The affected person should flush the eyes consistently for at least 15 minutes with the solution running at a rate of at least 1.51 litres per minute (LPM) and a temperature of around -15 to -37.7 degrees Celsius. Emergency eye washers can be portable or plumbed.
5 Tips on How to Choose Safe and Effective Emergency Eyewash Units
Australian Standards requirements are stringent, and eyewash solutions and delivery systems must meet high-quality standards. Every eyewash solution and delivery system is different and must meet the minimum workplace requirements for health and safety. So, how do you choose a safe and effective emergency eyewash unit?
1. Check for an AUST number
The Therapeutic Goods Administration (TGA) specifies that medications for therapeutic use must be included in the Australian Register of Therapeutic Goods (ARTG) and must have an AUST number. The AUST number should be clearly marked on the label. AUST numbers identify the drug’s labeller, the product itself, and the package size or quantity. The labeller also manufactures or distributes the medication. The TGA has approved medicines that appear in the ARTG. Checking the recall page on the TGA website can alert you to unsafe or recalled products.
2. Check the ingredients
The safest eye washing liquids are made with 100% sterilised water and sterilised saline — just enough saline so that the wash matches the human eye’s PH balance.
3. Ensure the fluid is sterile
Any product made for the human eye should be fit for its intended use—only source products from companies or countries with strict inspection requirements. You can use the search portal at MIMS to discover a breakdown of ingredients and review sterilisation procedures.
4. Check the expiration date
Products get tested at the time of manufacture and subsequently approved or denied. Among safety concerns, testing also gives information regarding the efficacy of a product and its shelf life. These standards and measurements are created and performed by the TGA because, over time, compounds found in certain drugs and solutions can break down, as can packaging. Once this occurs, the drug or solution can lose its ability to provide the therapeutic benefits intended — not to mention that it can even become unsafe.
5. Flush your eyewash stations regularly
It’s essential to flush your eye washer station to ensure ongoing sterilisation, especially in portable units. But even if your system is plumbed, your facility’s water system itself might be contaminated with pollutants such as limescale, rust, or other chemicals. It’s essential to change the fluid and regularly clean units to avoid accidental use of tainted eyewash solutions.
Safety First
It can pose dangers to your employees if they use eyewash that’s no longer sterile. Not only can this harm your workers, but it can also harm you and your business. Choosing a reputable eye washer manufacturer supplying TGA-approved units and sterile eyewash means you can offer your employees uninhibited access to a product that can help them in the event of an emergency. When your employees have a fast recovery, so does your company.
Ecospill has several eyewash units and solution products to help you keep your workers safe. Get in touch to learn more about Ecospill’s emergency eyewash units.